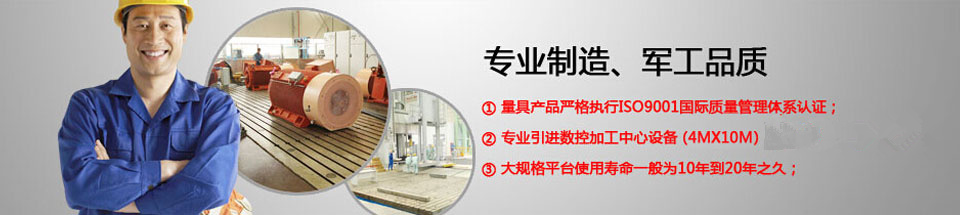
在鑄鐵行業(yè)中備受矚目的鑄鐵T型槽平臺及鑄鐵件中鑄造缺陷 - 夾渣的形成及影響因素。
唯有依照嚴(yán)格的技術(shù)參數(shù)進(jìn)行設(shè)計,嚴(yán)格把控生產(chǎn),才能得到質(zhì)量合格標(biāo)準(zhǔn)的鑄鐵T型槽平臺,從而才有鑄鐵T型槽平臺在機(jī)械制造、化工、五金、航空航天、石油、汽車制造、儀器儀表制造等行業(yè)中重要作用的體現(xiàn)。北重機(jī)械從建廠,十六年來一直嚴(yán)格自控把關(guān)產(chǎn)品質(zhì)量。
鑄鐵T型槽平臺上面加工有T型槽,用來固定工件、清理加工時產(chǎn)生的鐵屑或放以固定銷。它的相對兩個側(cè)面上,應(yīng)設(shè)置有安裝手柄、吊環(huán)等吊裝設(shè)施的螺紋孔或圓柱孔。設(shè)計吊裝位置時應(yīng)考慮盡量減少因吊裝而引起的變動。
以下便為大家簡述鑄鐵T型槽平臺及鑄鐵件中鑄造缺陷 - 夾渣的形成及影響因素。
鑄鐵T型槽平臺中石墨的形成過程稱為石墨化,如果鑄鐵的成分適當(dāng),且冷卻速度較緩慢時,且冷卻速度較緩慢時,碳將將以石墨形式直接從鐵水和奧氏體中析出。另外,石墨也可以由介穩(wěn)定相滲碳體分解而來,例如可鍛鑄鐵中的石墨就是白口鑄鐵在高溫退火時從滲碳體中析出來的。鑄鐵平板表面淬火的目的和方法:表面淬火的目的是提高鑄件的硬度和耐磨性。進(jìn)行表面淬火的鑄件,原始組織中的珠光體量應(yīng)大于65%,石墨細(xì)小并應(yīng)分布均勻。否則會因基體中鐵素體量過多,在快速加熱時奧氏體中溶碳量太少,致使淬火硬度不高。因此,如果基體組織中鐵素體量較多,應(yīng)在淬火前進(jìn)行一次正火處理,保證基體組織有足夠的珠光體,以獲得良好的表面淬火效果。鑄鐵T型槽平臺表面淬火的方法很多,有感應(yīng)加熱表面淬火、火焰加熱表面和電接觸加熱自冷表面淬火等方法。高頻率應(yīng)加熱表面淬火的淬硬層約為1毫米,硬度可達(dá)HRC50左右,中頻感應(yīng)加熱表面淬火的淬硬層可達(dá)3-4毫米,感應(yīng)加熱表面淬火具有質(zhì)量穩(wěn)定,變形小等優(yōu)點。鑄鐵T型槽平臺火焰表面淬火的淬硬層較深,一般可達(dá)2-8毫米,硬度HRC40-848,火焰表面淬火具有設(shè)備簡單、成本低廉、操作方便等優(yōu)點,適用于單件,小批或大型機(jī)床導(dǎo)軌的淬火,單淬硬度不易控制,容易過熱,淬火后變形大。
鑄鐵T型槽平臺鑄件夾渣的形成過程:球化處理時 Mg 、 RE 與鐵液中 O 、 S 反應(yīng)形成渣。當(dāng)鑄鐵T型槽平臺及鑄鐵件的鐵液溫度低、稀渣劑效果不佳、渣上浮不充分或扒渣不凈而殘留于鐵液中,此為一次渣。鐵液在運(yùn)輸、倒包、澆注、充型翻滾時氧化膜破碎并被卷入鑄型,在型內(nèi)上浮吸附硫化物聚集于上表面或死角處,此為二次渣。一般以二次渣為主。
影響鑄鐵T型槽平臺鑄件夾渣因素也分兩個方面為大家進(jìn)行講解,首先,形成一次渣的重要原因是在鑄鐵T型槽平臺鑄件夾渣的形成及鑄件中的原鐵液含硫量高、氧化嚴(yán)重。而,生成二次渣的主要原因是殘留鎂量過高,提高了氧化膜形成溫度。
鑄鐵T型槽平臺 及鑄鐵件中鑄造缺陷 - 夾渣形貌特征:分布于鑄件澆注位置上表面、型芯的下面及 鑄鐵平臺 或鑄鐵件的死角處,破斷面上顯現(xiàn)暗黑色無光澤深淺不一的夾雜物,斷續(xù)分布。金相觀察可見條狀、塊狀、夾雜物。臨近的石墨可呈片狀或球狀。磁粉探傷時磁痕呈條狀分布,條紋多而粗、堆積密表明夾渣嚴(yán)重。電子探針分析表明夾渣含 Mg 、 Si 、 O 、 S 、 Ce 、 A1 等,是由硅酸鎂、氧硫化合物、鎂尖晶石等組成。
系統(tǒng)地認(rèn)識鑄鐵T型槽平臺的基本特性,了解澆鑄過程中形成鑄件夾砂的原因、特性以及造成該缺陷的影響因素和形貌特征,為更透徹地研究鑄鐵T型槽平臺提供更有效的理論基礎(chǔ),旨為提供更優(yōu)質(zhì)高性能的鑄鐵T型槽平臺。同樣希望,像我們威岳機(jī)械所致力推崇的,高強(qiáng)度高精度高耐磨高穩(wěn)定性的鑄鐵T型槽平臺能被更廣泛地應(yīng)用于各行業(yè)作業(yè)中。
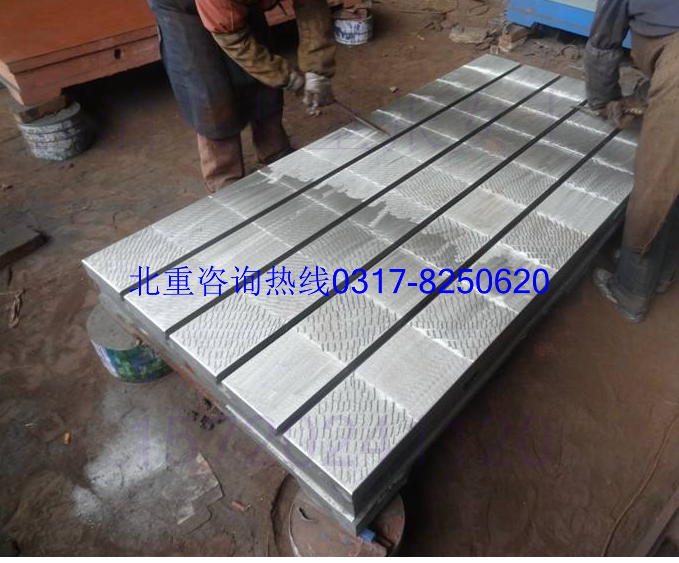